Operational Efficiency Assessment
Comprehensive analysis and optimization of organizational processes through systematic evaluation, workflow redesign, and performance enhancement methodologies delivering measurable productivity improvements.
Back to Home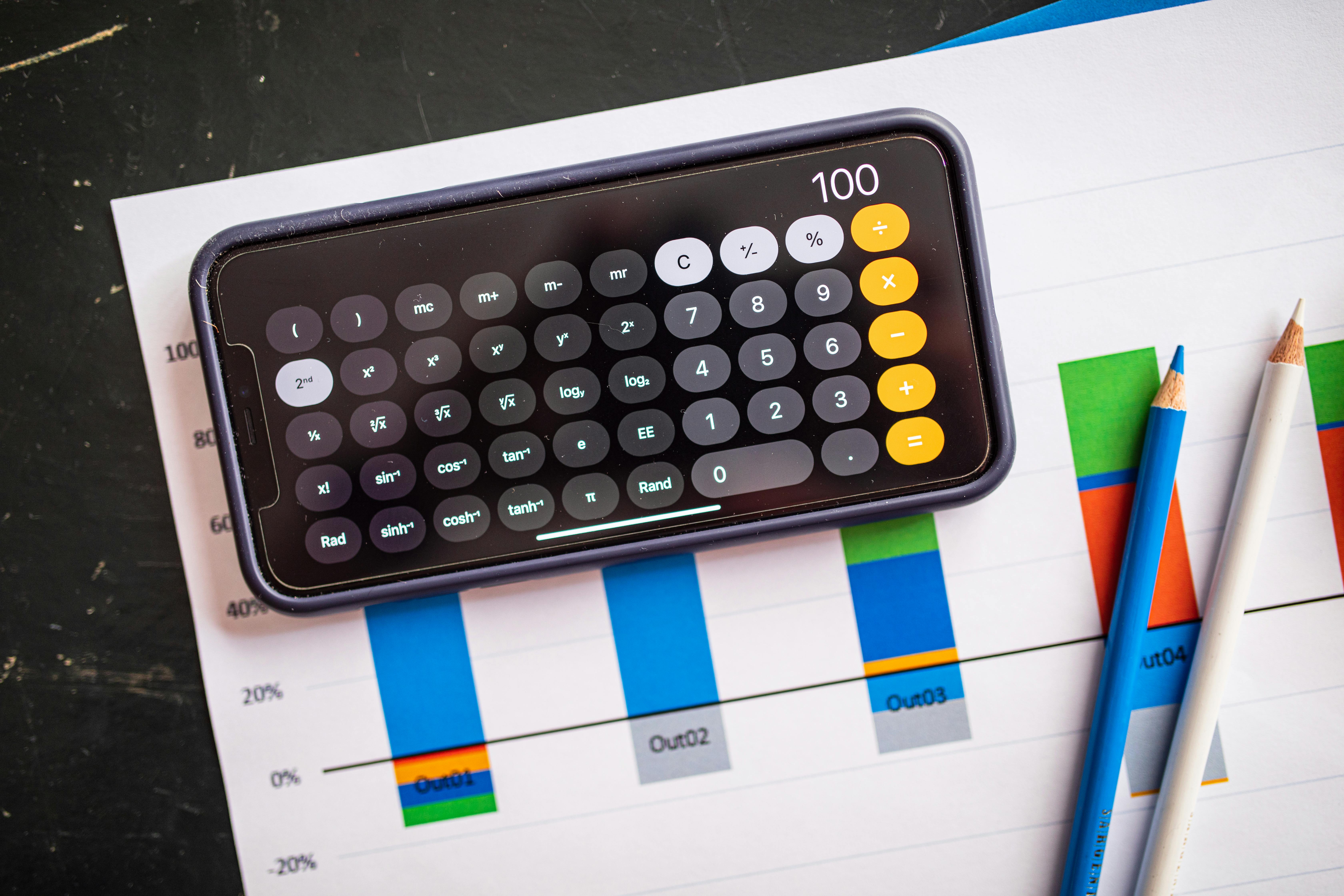
Comprehensive Operational Assessment
Our operational efficiency assessment provides systematic evaluation of organizational processes, identifying bottlenecks, redundancies, and optimization opportunities through data-driven analysis and industry-proven methodologies.
Service Benefits
Process Optimization
Streamlined workflows with eliminated redundancies
Resource Utilization
Optimal allocation of human and material resources
Quality Enhancement
Improved output quality through systematic controls
Productivity Increase
25-45% improvement in operational throughput
Cost Reduction
15-30% operational cost savings
Scalability Framework
Sustainable growth-ready operational structure
Expected Outcomes
Technical Methodology & Approach
Our systematic approach combines internationally recognized frameworks with proven analytical techniques, ensuring comprehensive evaluation and sustainable improvements.
Process Mapping
Comprehensive documentation of current workflows using BPMN standards and value stream mapping techniques for complete process visualization.
Statistical Analysis
Lean Six Sigma methodologies with DMAIC framework application for data-driven problem identification and solution validation.
Optimization Design
Advanced process redesign using constraint theory, workflow optimization algorithms, and resource allocation modeling for maximum efficiency.
Systematic Implementation Framework
Assessment Phase
Current state analysis, stakeholder interviews, process documentation, and baseline measurement establishment.
Analysis Phase
Data collection, statistical evaluation, bottleneck identification, and improvement opportunity prioritization.
Design Phase
Solution architecture, process redesign, optimization modeling, and implementation planning.
Implementation
Controlled deployment, performance monitoring, adjustment protocols, and sustainability planning.
Results & Success Stories
Demonstrable outcomes across diverse industries showcasing the measurable impact of our operational efficiency assessment methodology.
Manufacturing Sector
Mid-size production facility
"Process optimization resulted in €185,000 annual savings while improving product quality and employee satisfaction significantly."
Service Industry
Professional services firm
"Streamlined workflows enabled 30% capacity increase without additional staff, improving both profitability and service quality."
Technology Sector
Software development company
"Agile process optimization improved delivery predictability and team productivity, resulting in 25% faster time-to-market."
Aggregate Results Across All Engagements
Process Details & Timeline
Step-by-step implementation process with clear deliverables, milestones, and timelines ensuring transparent progress tracking and successful outcomes.
Initial Assessment & Scoping
Weeks 1-2Activities
- • Stakeholder interviews and requirements gathering
- • Organizational structure and process mapping
- • Current state documentation and baseline measurement
- • Resource availability assessment and planning
Deliverables
- • Project scope and methodology document
- • Current state process maps
- • Baseline performance metrics report
- • Implementation timeline and resource plan
Data Collection & Analysis
Weeks 3-6Activities
- • Comprehensive data collection and measurement
- • Statistical analysis and trend identification
- • Bottleneck analysis and constraint identification
- • Benchmarking against industry standards
Deliverables
- • Detailed analytical findings report
- • Process performance dashboard
- • Gap analysis and opportunity matrix
- • Benchmarking comparison study
Solution Design & Optimization
Weeks 7-10Activities
- • Optimized process design and workflow modeling
- • Resource allocation optimization and planning
- • Quality control framework development
- • Change management strategy formulation
Deliverables
- • Optimized process architecture
- • Implementation roadmap and action plan
- • Quality assurance protocols
- • Change management guidelines
Implementation & Validation
Weeks 11-16Activities
- • Pilot implementation and testing protocols
- • Full-scale deployment and monitoring
- • Performance validation and adjustment
- • Team training and knowledge transfer
Deliverables
- • Implementation completion report
- • Performance improvement validation
- • Training materials and documentation
- • Continuous improvement framework
Complete Service Portfolio
Comprehensive business optimization solutions designed to work individually or in combination for maximum organizational transformation.
Operational Efficiency Assessment
Process optimization and workflow enhancement
- 25-45% efficiency improvement
- 15-30% cost reduction
- 8-16 weeks implementation
Cost Reduction Strategy
Financial optimization and expense management
- 20-40% cost reduction
- 6-12 months ROI
- €150K+ annual savings
Performance Improvement
Strategic KPI development and monitoring
- 30-60% performance boost
- 90% goal achievement
- 12-20 weeks implementation
Professional Tools & Techniques
Industry-leading analytical tools and methodologies ensuring precise assessment, accurate modeling, and effective implementation of operational improvements.
Process Mining Software
Advanced analytics for process discovery and performance measurement
Statistical Analysis Suite
Six Sigma tools for data analysis and performance validation
Simulation Modeling
Monte Carlo and discrete event simulation for optimization
BPMN Documentation
Standardized process notation for clear workflow mapping
Technology Stack & Equipment
Software & Platforms
Microsoft Visio Professional
Process mapping and workflow visualization
Minitab Statistical Software
Six Sigma analysis and quality control
Arena Simulation
Process modeling and scenario analysis
Tableau Analytics
Data visualization and dashboard creation
Measurement & Analysis
Time & Motion Study Equipment
Precision timing and workflow analysis
Digital Data Loggers
Automated performance data collection
Mobile Assessment Tablets
Real-time data capture and documentation
Video Analysis Systems
Detailed workflow observation and review
Safety Protocols & Standards
Comprehensive safety and compliance framework ensuring minimal risk, data protection, and adherence to international business consulting standards.
Risk Management Framework
Business Continuity Protection
Comprehensive protocols ensuring zero disruption to critical business operations during assessment phases.
Data Security Compliance
GDPR-compliant data handling with encrypted storage, controlled access, and secure transmission protocols.
Quality Assurance Standards
ISO 9001:2015 certified processes with continuous quality monitoring and improvement protocols.
Professional Indemnity Coverage
Comprehensive professional liability insurance providing full protection for all consulting engagements.
Compliance Certifications
ISO 9001:2015
Quality Management
EU 2016/679
Data Protection
PMP Certified
Project Management
Black Belt
Lean Six Sigma
Target Audience & Use Cases
Operational efficiency assessment serves diverse organizational types and scenarios, delivering tailored solutions for specific business requirements and operational challenges.
Manufacturing Companies
Ideal For:
- • Production facilities with 50-500 employees
- • Annual revenue €5M-€50M
- • Complex multi-stage processes
- • Quality control challenges
Common Challenges:
- • Production bottlenecks
- • Inventory optimization
- • Equipment utilization
- • Waste reduction needs
Service Organizations
Ideal For:
- • Professional service firms
- • Healthcare facilities
- • Financial institutions
- • Consulting companies
Common Challenges:
- • Client processing delays
- • Administrative inefficiencies
- • Resource scheduling issues
- • Service quality consistency
Growing Businesses
Ideal For:
- • Rapidly expanding companies
- • Family-owned businesses
- • Acquisition targets
- • Scale-up phase organizations
Common Challenges:
- • Scaling operational processes
- • Maintaining quality during growth
- • System integration needs
- • Standardization requirements
When to Consider Operational Efficiency Assessment
Key Indicators
Expected Benefits by Industry
Results Measurement & Tracking
Comprehensive measurement framework with real-time tracking, detailed analytics, and continuous performance monitoring ensuring sustainable improvements and ROI validation.
Key Performance Indicators
Average reduction in end-to-end process completion time
Improvement in overall resource allocation efficiency
Enhancement in output quality and error reduction
Decrease in operational cost per unit of output
Real-Time Dashboard Metrics
Automated Reporting
Daily, weekly, and monthly automated performance reports with trend analysis and actionable insights.
Alert System
Proactive notifications for performance deviations, threshold breaches, and optimization opportunities.
Benchmarking
Comparative analysis against industry standards and best-in-class performance metrics.
Follow-up & Maintenance Support
Comprehensive post-implementation support ensuring sustained benefits, continuous optimization, and long-term performance maintenance through structured follow-up protocols.
Support Timeline & Activities
30-Day Post-Implementation Review
Comprehensive performance validation, initial results analysis, and optimization adjustments based on operational feedback.
- • Performance metrics validation
- • Process fine-tuning adjustments
- • Team feedback integration
- • Initial ROI calculation
90-Day Sustainability Assessment
Detailed evaluation of process adherence, performance maintenance, and identification of additional optimization opportunities.
- • Sustainability metrics review
- • Performance trend analysis
- • Additional training needs assessment
- • Continuous improvement planning
Annual Performance Optimization
Comprehensive yearly review with strategic recommendations for next-level improvements and organizational evolution.
- • Annual ROI calculation and validation
- • Strategic optimization recommendations
- • Technology upgrade assessments
- • Future roadmap development
Ongoing Support Services
24/7 Support Hotline
Direct access to expert consultants for urgent issues and immediate guidance on process concerns.
Knowledge Base Access
Comprehensive resource library with process documentation, best practices, and troubleshooting guides.
Team Training Updates
Quarterly training sessions for new team members and refresher courses for existing staff.
Performance Reviews
Monthly performance check-ins with detailed analytics and optimization recommendations.
Extended Support Options
Premium Support
Enhanced support with priority response, dedicated consultant, and monthly optimization reviews.
Standard Support
Regular support with quarterly reviews, email assistance, and knowledge base access.
Basic Support
Essential support with bi-annual reviews, documentation access, and email support.
Frequently Asked Questions
Comprehensive answers about operational efficiency assessment process, implementation, and expected outcomes.
How long does a typical operational efficiency assessment take to complete?
The complete assessment and implementation process typically spans 8-16 weeks, depending on organizational complexity and scope. This includes 2 weeks for initial assessment, 4 weeks for data collection and analysis, 4 weeks for solution design, and 4-6 weeks for implementation and validation. We provide detailed timeline projections during the initial consultation.
What level of disruption should we expect during the assessment process?
Our methodology is specifically designed to minimize operational disruption. Most assessment activities occur during normal business hours with minimal impact on daily operations. Critical process changes are implemented during planned maintenance windows or low-activity periods, ensuring business continuity throughout the engagement.
How do you measure and guarantee the promised efficiency improvements?
We establish baseline measurements before implementation and track improvements using quantitative metrics including process cycle time, resource utilization rates, quality scores, and cost per unit. Our performance guarantees are backed by measurable KPIs and we provide real-time dashboards for continuous monitoring. We offer result-based pricing options for qualified engagements.
What staff involvement is required from our organization during the assessment?
Successful implementation requires active participation from key stakeholders including process owners, operational teams, and management. We typically recommend allocating 10-15% of relevant personnel time during assessment phases and 15-20% during implementation. We provide comprehensive training and change management support to ensure smooth adoption.
Can the assessment be customized for our specific industry requirements?
Absolutely. Our methodology is adapted to meet specific industry requirements including regulatory compliance, safety standards, and sector-specific best practices. We have extensive experience across manufacturing, healthcare, financial services, technology, and professional services sectors, ensuring industry-relevant solutions.
What happens if the projected improvements are not achieved?
We provide performance guarantees based on agreed baseline measurements and targets. If projected improvements are not achieved within the specified timeframe, we continue working at no additional cost until targets are met, or provide partial refunds based on actual results achieved. Our professional indemnity insurance covers all service commitments.
How do you ensure the improvements are sustainable long-term?
Sustainability is built into our methodology through comprehensive training programs, documentation systems, continuous improvement frameworks, and follow-up support. We establish monitoring mechanisms, create performance dashboards, and provide 90-day post-implementation support to ensure lasting benefits and ongoing optimization.
What makes your approach different from other efficiency consulting services?
Our Swiss-methodology approach combines rigorous analytical frameworks with practical implementation focus. We use advanced process mining software, statistical analysis tools, and proven methodologies like Lean Six Sigma. Our emphasis on measurable outcomes, comprehensive follow-up support, and industry-specific customization ensures superior results and client satisfaction.
Optimize Your Operations Today
Transform your operational efficiency with proven methodologies, expert analysis, and measurable results. Start your optimization journey with a comprehensive assessment.
Get Started Now